Wine logistics: Today, organization and timing are paramount
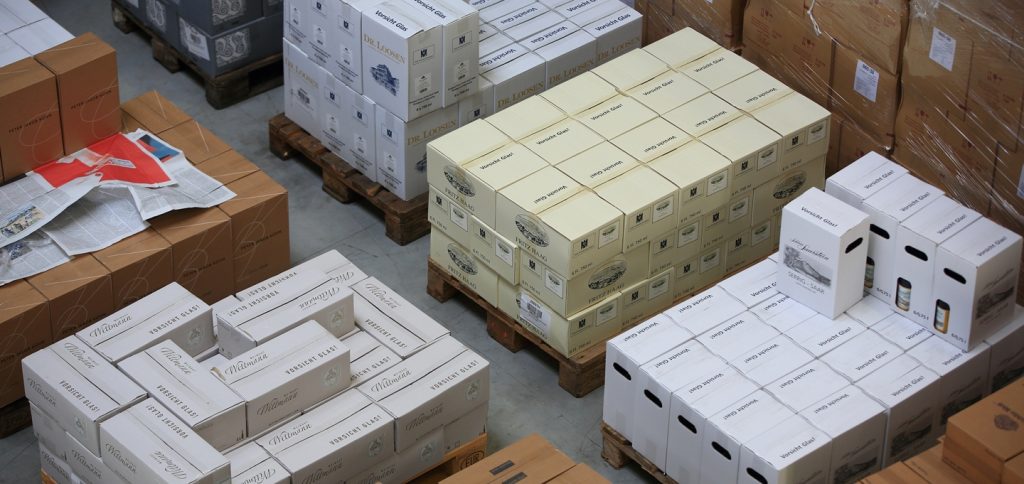
Like in many other business sectors, logistics is a key issue in the wine industry. Wine logistics is both a cost factor and a business challenge and requires well-thought-out organization, the use of the latest technology, fleet solutions and complex IT systems at every level.
Transportation is essential, as wine is no longer only consumed where the base wines are produced. Today wine is generally bottled in locations other than where it’s distributed. Most wine is consumed in major urban areas and big cities and has to be transported there to begin with.
Wine logistics and transportation: from raw ingredients to the finished product
The amount of wine that is sold has grown over the years thanks to the liberalization of global trade and the removal of customs and trade barriers. The volume of wine exported in bulk and in barrels across international borders now totals more than 100 million hectoliters. This accounts for more than one third of total global wine production, which is approx. 250 million hectoliters.
Wine logistics and transportation comprise three stages, from the raw ingredients to the finished product:
- delivery of wine transported in bulk and in barrels by tanker or with containers and flexitanks to the winery;
- in-house logistics and storage; and
- haulage and delivery logistics for the bottled and packaged wines.
Flexitanks are becoming increasingly popular all around the world
While cider and new wine still in fermentation are transported within the European wine-producing regions to the processing facilities by tanker, “flexitanks” have made a real name for themselves in international trade. Flexitanks are now indispensable in particular for wines which are transported in shipping containers from overseas to large bottling wineries in Europe.
The systems are comprised of two components: a liquid-tight steel container and a specially manufactured woven fabric layer into which the wine in question is flowed, ready for shipping. They are available as 20- and 40-foot containers with capacities of around 20,000 to 50,000 liters, respectively. This means that wine can be easily shipped from the production wineries in Chile, Argentina, Australia and South Africa by sea container to Europe. The containers are then transported by tractor-trailer truck from the ports on the North Sea coast to the major bottling wineries in France, Germany and other European countries.
More economical, lighter and more environmentally friendly
The use of flexitanks and the shipment of loose wine in bulk instead of pre-filled wine bottles significantly reduces weight and transport volumes and results in a much smaller carbon footprint. The cost of overseas transport is 15 to 18 cents per liter, therefore often making it a considerably more economical option than transporting wines by tanker from one end of Europe to another. After all, the high tolls charged on roads and highways and the haulage costs make a significant difference.
For wineries specializing in the bottling of wines, having efficient, streamlined in-house wine logistics is a must. Cost-effectively filling wine bottles and containers of all shapes and sizes that are made from different materials is what they pride themselves on doing best. These days, wine is filled in glass bottles (usually 0.75 and 1.0-liter bottles) and carton packaging such as 1-liter Tetra Paks and 1.5 and 3.0-liter foil bags inside cardboard containers. From an organizational perspective, they have to bring together all the necessary materials – glass bottles, corks, screw tops, labels and packaging materials such as carton and cardboard packaging and pallets, as well as the wine that goes into them.
Organization, IT-supported documentation and control
Because of the various pieces of equipment and packaging sizes available, several different finished products can be made from one single product, which only serves to further compound the logistical challenges that producers face when it comes to operational storage. As gatekeepers via-à-vis consumers, trading companies demand a wide variety of different versions and formats in line with their logistical and trade-specific requirements. Time also plays a decisive role, which means that super-efficient storage systems are essential for managing a broad range of different products efficiently.
Modern, fully-automated high-rise storage systems as well as driverless fork-lift trucks and industrial trucks are now part and parcel of the state-of-the-art equipment used in many wineries. In the wine industry, product-specific requirements in terms of temperature-controlled storage and logistics also have to be met. As the goods in question are perishable, the first-in, first-out (FIFO) principle is used for all wine storage systems. Uninterrupted stock control as well as the need to ensure permanent delivery capacity increase the complexity of all the logistics involved.
Logistics and distribution in the wine industry these days require a significant amount of organization and IT-supported documentation and control – both in the case of shipping containers from overseas to European wineries as well as storing finished products at bottling and filling facilities and making B2B and B2C deliveries.