Plastics: Where do bottles end up?
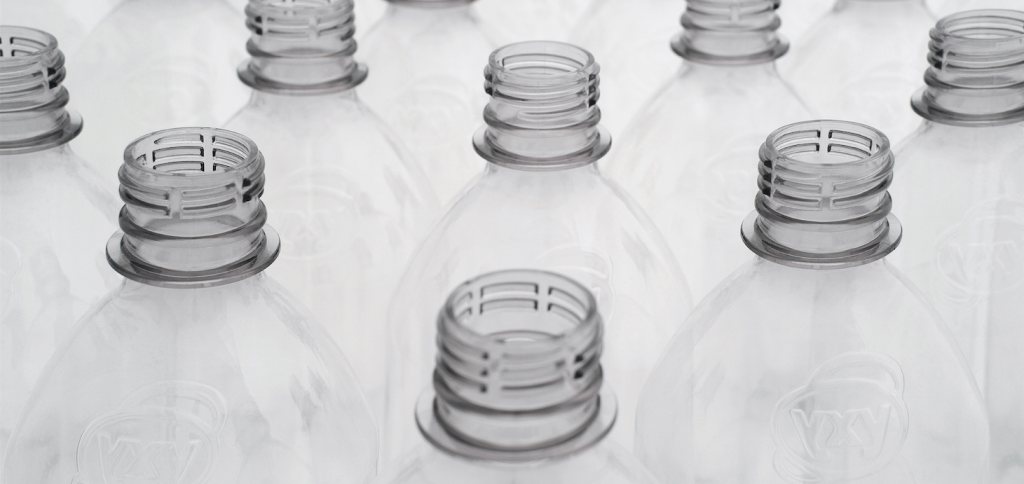
“If we don’t change the way we produce and use plastics, there will be more plastics than fish in our oceans by 2050,” warns Frans Timmermans, First Vice-President and EU Commissioner for Better Regulation, Interinstitutional Relations, the Rule of Law and the Charter of Fundamental Rights in the Juncker Commission.
In Europe alone, 25 million tons of plastic waste is generated every year – and less than 30 percent of this is collected for recycling. In that light, Timmermans’ 2050 scenario is indeed conceivable. The topic is now being addressed with the help of a new EU-wide strategy for plastics, according to which all plastic packaging in the EU market should be recyclable as of 2030. It’s a major step that must be backed up by a change in thinking – within the beverage industry, too, with all its plastic beverage bottles.
Strongly growing market for bioplastics
In this context, bioplastics are becoming increasingly popular. Estimates suggest that the market for bioplastics will grow by 20 percent over the next five years alone. The European Bioplastics Association has forecast an increase in worldwide production capacity for bioplastics from approximately 2.05 million metric tons in 2017 to about 2.44 tons in 2022. “Ultimately, increased consumer awareness for sustainable products and packaging is contributing to this growth,” believes Francois de Bie, Chairman of European Bioplastics.
The big names in the nonalcoholic beverage industry are thinking strategically
Many major players in the beverage industry have a very positive attitude toward bioplastics. For example, PepsiCo plans to increase its use of bio-based materials and, by 2025, use only recyclable or compostable packaging. “Bioplastics are key elements of our sustainable packaging strategy,” explains Sandeep Kulkarni, Senior Principal Scientist at PepsiCo.
Danone and Nestlé Waters plan to put a beverage bottle made from 100 percent bio-based PET on the market by 2020. For this purpose, the two companies have joined forces with the American startup Origin Materials to form the NaturAll Bottle Alliance. Origin Materials developed a method for processing raw materials made from lignocellulose, especially from scrap paper, sawdust, and woodchips. The company wants to produce Bio-PTA from the biomass to replace 70 percent of the PTA in PET, which is currently only synthesized from fossil raw materials. The second component of PET, monoethylene glycol, can already be produced from renewable raw materials.
PEF has many benefits
Nevertheless, the industry appears to be focusing more on a new polymer: PEF, which is 100 percent bio-based and, compared to PET, has better barrier and thermal properties. The result: Nonalcoholic beverages in PEF bottles last longer. At the same time, PEF bottles can have thinner walls than classic PET bottles, which means less packaging material.
The focus is on the production of PEF at Amsterdam’s Synvina, a joint venture established by BASF and Avantium to produce and market furandicarboxylic acid (FDCA) from renewable raw materials and to market the new polymer polyethylene furanoate (PEF) from the chemical building block FDCA. To produce FDCA, Synvina will use the YXY process developed by Avantium, which is based on fructose as a renewable raw material. A major success for Synvina is the European PET Bottle Platform’s interim approval for the disposal of PEF bottles via existing recovery systems for PET, which applies to the volume of PEF that can be produced with the help of Synvina’s planned 50,000-ton reference plant for FDCA.
New plastics: Alternative production approaches
But there are other approaches for producing PEF apart from Synvina’s method. For example, scientists at the University of Hohenheim produce untreated hydroxymethylfurfural (HMF) from chicory roots, which can then be used to produce PEF bottles. Scientists at the Thünen Institute for Rural Areas, Forestry and Fisheries have also developed a new process to produce HMF based on an innovative extraction agent called hexafluoroisopropanol (HFIP). According to the scientists, much more HMF can be extracted with HFIP – a 90 percent yield, they claim – than with the substances that were previously used. The reaction can take place in water as a solvent. And since the boiling point of HFIP is 58 degrees Celsius, it can be recovered after the reaction through distillation in an energy-saving process. The aqueous reaction phase can also be reused.
The approach taken by scientists at Standford University in California is also interesting. To produce the precursor FDCA (furandicarboxylic acid), they use “inedible plant material” such as grass and waste that remains after harvesting, as well as carbonate and CO2. In this method, furan-2-carboxylic acid is produced from plant material, mixed with cesium carbonate (a salt containing carbon recovered from limestone), and melted with the addition of CO2. After about five hours, 89 percent of the molten material has converted to FDCA, which can then be processed to PEF.
The future offers many options
We can assume that in the future, scientific activity will also produce other possibilities for producing bioplastics that are suitable for beverage containers. We will just have to wait and see whether PET bottles will be replaced in the medium to long term or if the new plastic variants are just another alternative.