The future of the beverage industry: Flexibility as a competitive factor
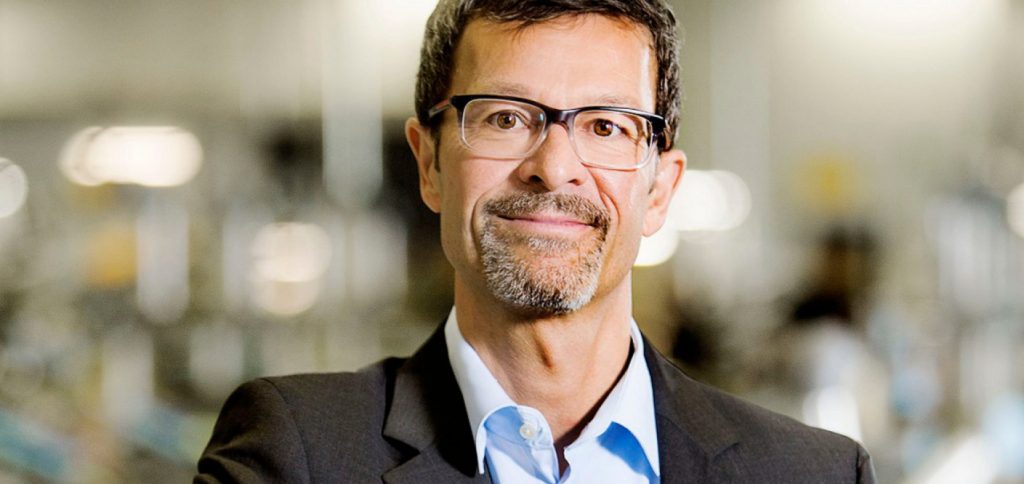
Highly efficient technology that adapts to new conditions and customers’ wishes simply and quickly – this is what the non-alcoholic beverage industry wants. In this regard, flexibility is playing an increasingly important role – ideally, flexibility achieved with compact and space-saving machine concepts. Supplier industries offer interesting options. One that is increasingly attracting attention is the new generation of robots.
“More in one” – The potential of flexible concepts
Karl-Heinz Klumpe, Product Manager Packaging at KHS in Kleve, puts it in a nutshell: “If two or more individual machines can be combined to provide a block solution, the user gains several advantages.” For example, using its InnoDry Block, the company combines the secondary-packaging production steps and the tertiary packaging steps; packaging and palletizing are handled within one process. The flexibility of buffer areas and a dynamic manipulation system for exact positioning on the pallet make this possible. Company data confirms that this block solution – with its short transport distances, reduced maintenance costs and fast changeover times – offers advantages.
Krones is also relying on compact, flexible packaging technology in keeping with the “more in one” motto. Take its Variolone, for example: The machine first places individual containers in multipack containers and then places them in the respective sales or outer packaging. The modular system comprises three modules – cartoner, feeding and base module – which can be combined to form an individual packaging line. The system replaces up to six conventional single machines with conveying technology. Here, too, benefits such as space savings, lower maintenance requirements and fewer operators are worth mentioning in addition to the obvious advantage of flexibility.
In general, the challenge the supplier industry faces is integrating an increasing number of functions into a single compact technical solution in order to combine as many work areas as possible and within reason – and, as these examples illustrate, with results that outperform conventional concepts in many respects.
Future-oriented experiments
Sometimes ideas are considered long before their practical implementation comes into focus. For example, CSi industries B.V., which specializes in production-environment conveyor technology, experimented with technical possibilities that might be available in the future. One example was a drone that picks up and places cartons. The company finds it unlikely that the next generation of palletizers will be based on drones, but in its view, every innovative application takes manufacturers one step further toward finding alternative, newer and more innovative solutions. This is a fascinating approach when we consider that what seems highly unlikely now may become probable in future.
And speaking of the future: Cobots are coming
But for the moment, let’s talk about robots. According to predictions, conventional robots and especially the new robot generation, cobots (collaborative robots), have a promising future in all production areas, including the non-alcoholic beverage industry. The 2017 World Robot Report states that the number of industrial robots will rise to over three million by 2020, with some 1.9 million robots in use in Asia alone by that time. To put that in perspective: In 2016, there were around 1.8 million industrial robots in use worldwide. Joe Gemma, President of the International Federation of Robotics (IFR) says: “Robots operate with the highest precision and will play a key role in new digital production environments when networked with the Internet of Things (IoT). The rapidly growing range of models extends the application possibilities for industrial robots and offers companies of all sizes the opportunity to automate flexibly.”
In fact, numerous suppliers are already working on developing and perfecting robots that work directly with people and can be perceived as helpful colleagues. These robots, called cobots, are equipped with sensors. Universal Robots, for example, has developed six-axis articulated robots in various sizes and with varying load-bearing capacities that can work directly next to their human coworkers, either without or with minimal protective devices. They can also be used in small and medium-sized companies. Speaking on the future chances of these unusual “colleagues”, Helmut Schmid, Managing Director and General Manager Western Europe of Universal Robots said: “Irrespective of the task – pick and place, packaging, labeling or palletizing – we see enormous potential for lightweight robotics and human-robot collaboration in packaging and logistics in the coming years.” Kuka too, is venturing down new robot-driven paths with Optoforce. Ákos Dömötör, CEO Optoforce, said: “Our six-axis touch sensors are combined with a comprehensive software package. While the sensor hardware gives the robots sensitivity, the software transforms this sense of touch into industrial applications.” In concrete terms, this involves manual guidance, position detection and centering for Kuka robots with payloads of up to 16 kilograms.
Smart factory and predictive maintenance in the beverage industry
Even smarter solutions are leading to another future trend: the digitally networked, intelligent factory, known as the smart factory. According to experts, predictive maintenance will also play an increasingly important role here. Speaking at DLG Trendmonitor 2018, Matthias Heinrich, POD Manager Digital Solutions, GEA Westfalia Separator Group, said: “Within the next six years, predictive maintenance and smart factory concepts will merge more and more. They will jointly be perceived as the driving force.” Dr. Sabine Brunklaus, Department Life Science Technologies Institute for Food Technology NRW, Ostwestfalen-Lippe University of Applied Sciences, added: “In six years, predictive maintenance technology should be mature enough to offer new equipment with a predictive maintenance system as a standard option.” The smart food factory, on the other hand, belongs to the distant future, in her view. “The trend is clearly moving in this direction, but given the current state of science and technology, a comprehensive smart factory concept will not be implemented within the next six years, at least in industrial food production.”
Flexibility means acting, not reacting
It’s a matter of wait and see. After all, many new ideas have bypassed predicted development times. And that’s why our recommendation for the non-alcoholic beverage industry is: Keep up with the times and keep a watchful eye on smart-factory developments in order to ensure you don’t miss out on competitive disadvantages because you were late to integrate new solutions offering enhanced flexibility and efficiency advantages.