Brewery-based Soda Production
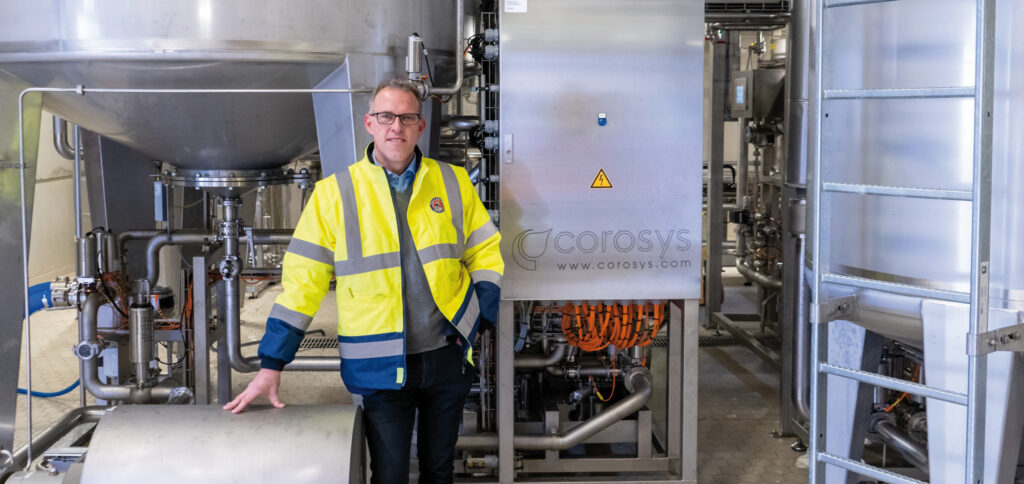
It’s already been seven years since the Paulaner Brewery left its old brewing premises in Nockherberg and moved to Langwied in Munich, yet people still refer to it as the “new” brewery. However, some of the facilities and systems were also relocated from Nockherberg and incorporated into the new premises, such as the mixing system for mixed beer beverages and non-alcoholic beverages. These segments in particular are growth areas in the beer market, and the popularity of Paulaner’s products meant that capacity needed to be seriously ramped up. Ole Kohls, Marketing Manager at corosys beverage technology, explains how this was achieved with the installation of a new mixing system.
Non-alcoholic beers, mixed beer beverages, and soft drinks in vogue
The German beverage market has experienced two trends in recent years: Sales of alcoholic beers are declining while non-alcoholic beverages (including non-alcoholic beers) are performing well. The Paulaner Brewery is a traditional Bavarian brewery with a wide range of specialty beers. Lager, which is really booming at the moment, has been brewed by the company for 125 years. But the trend toward non-alcoholic beverages has also been recognized, and the range also includes non-alcoholic beers and mixed beer beverages, as well as soft drinks.
Paulaner Spezi, which features a very on-trend retro design, has also been available as a zero version since the start of the year. Popular mixed beer beverages, such as Paulaner Lemon Wheat Beer or the Natural Radler (Shandy) sold under the Hacker-Pschorr brand, are also available both with and without alcoholic. These beverages are the Paulaner Brewery Group’s answer to current market trends, and their success has now led it to also make some changes to its plant technology.
An expanding product range requires cutting-edge brewing facilities
The expanding product range coupled with growing demand also calls for a cutting-edge brewery like the one in Langwied in Munich, especially for mixed beverages. “Our annual production figures for soft drinks are growing considerably year on year. Paulaner Spezi accounts for a large part of that and the launch of Paulaner Spezi Zero has proven to be a big success,” says Christian Dahncke, the Paulaner Brewery Group’s Chief Master Brewer. “New mixed beer beverages have been added in recent years and these have also seen considerable growth in sales.” So it wasn’t a matter of whether the company would invest in upgrading the mixing system that had been relocated from Nockherberg to the new brewery, but rather when. Plans had already been made to expand the system. “Our forecasts clearly showed that we would reach our capacity limits with the old line, in particular during seasonal peaks when demand is particularly high and we need to produce various mixed beverages at the same time. We have six filling lines which we want to use intermittently directly from the mixer,” says Christian Dahncke. “It was therefore clear that, if we wanted to keep pace with growing demand, we would have to ensure that our products were not competing with each other in the production and filling processes. Two large mixing systems provide us with the flexibility we need.”
2020 call for tenders and contract award
The call for tenders for the new mixing system was issued in 2020. The requirements for the new system were, on the one hand, a broad output range of 150 hl/h to 450 hl/h, but also a switch from IBC containers to a supply of raw materials via tanker trucks. A system was needed that could produce a peak of 400 hl/h to 420 hl/h, with that output not designed to flow straight into the filling lines but be temporarily stored in pressure tanks. On the other hand, reduced output of 120 hl/h to 150 hl/h would also have to be possible for supplying the filler directly. “Probably the most challenging part of the tender process was covering this output range and managing to make an optimally mixed product with the dosing technology and continuously good carbonization,” says Dahncke. “However, the switch from raw materials in small containers to tank delivery was also a concern.” Two concentrate tanks were to be built to enable that. It was also clear that all of the systems involved would have to be fully automated, which covers the entire process of delivery, recording of quantities and transfer of data into the ERP system so that billing can be carried out there directly. Paulaner took care of the automation side of things itself but that demanded the metrological requirements and the process design. A willingness to go the extra mile was required to meet another requirement, namely full integration into the existing control and visualization system known as Krones Botec.

Finally, the existing system also needed to be fitted with a new CO2 injector in order to dose the carbon dioxide into both systems in the same way. “One of our quality requirements involves setting CO2 content with pinpoint accuracy.” In order to ensure that, according to Dahncke, it was time to replace the carbonization unit of the old system on account of its age. “Otherwise, more extensive maintenance work would have been required. In the end, we decided to use the same injector for both systems.”
The contract award stage of the project was also carried out in 2020. Ultimately, corosys beverage technology edged out four competitors by submitting the best bid for meeting the extensive requirements covering different areas of expertise. “The decision wasn’t just based on value for money,” says Dahncke, explaining why the contract was awarded to the Hessen-based company. “We were also extremely impressed with corosys’ in-line carbonization, in other words, the carbonization method involved, which offered a real advantage over their competition.” corosys was also a trusted partner as the client had already used the plant manufacturer’s water deaeration systems in the past which now also supply the mixing system, including the blending and carbonization system, with deaerated water.
The CoroBev mixing system
The new method for receiving raw materials from a tanker truck now feeds them into the two concentrate tanks, each with a net holding capacity of 250 hl. Thanks to the leak-proof valves and the corresponding circuit, continuous production can be achieved even during the receipt process and cleaning. Thanks to an additional raw materials line to the existing system, it is also possible to mix beverages from the tank in this system or in both systems simultaneously. Sugar and raw materials are each dosed via a control section with two control valves of differing sizes installed in parallel. They proportionally adapt the flow rate of the liquid to be dosed in line with the volumetric flow rate of the deaerated water as a basic flow with extreme precision. The mixture is then cooled and subsequently carbonized in the gas dispersion injector (GDI) that corosys developed itself. The GDI, which was installed in both the new and existing system, is a prime example of how precision engineering and a sound understanding of physics can be combined to produce efficient solutions.

“The injector, which is installed in all corosys gas-dissolving systems, functions without any fittings, such as frits or static mixers, etc., since the dissolution of the CO2 relies solely on the Venturi effect,” explains corosys Sales Manager Stefan Meyering. Thanks to the optimized flow in the injector, the beverage to be carbonized is very uniformly mixed with the CO2, which is divided up into tiny little bubbles by the turbulence caused by the injector, ensuring that the CO2 is fully dissolved in the subsequent holding section. The even distribution of the CO2 can be monitored via an inspection glass at the start of the dissolution section.
Essential quality control is carried out after the dissolution section in an inline measurement tool for CO2, sugar content for sodas, but also additionally original wort and alcohol for mixed beer beverages. The measurement tool is located in the recirculation section of the buffer tank to ensure that optimally mixed product is always provided to the filling system. It is also possible to circulate via the bypass of the system’s buffer tank and hence prevent any start-up losses.
Implementing the project during ongoing operation
Implementing the project in 2021 was of course also affected by the pandemic. The face-to-face meetings required at the start of the project were kept to a minimum, and project members communicated digitally where possible. This included project meetings but also general exchanges, in particular discussions regarding process descriptions, joint work on programming and much more. “We made the best use of digital communication methods,” confirms Christian Dahncke. Another partner was involved in the project for the infrastructure work and pipework, but even though three different companies were involved, they still managed to closely coordinate everything during the pandemic.

corosys was also heavily involved in the process optimization of the simultaneous upgrade of the valve manifold, since this was integrated into the entire process. “The valve manifold was upgraded to connect the mixer to the pressure tanks. That involved building a new filling line in the pressure tank cellar,” says Dahncke, explaining the step. He also highlights the huge challenge involved in connecting the pressure tanks via DN100 double-seated valves, which, like the installation of the mixing system, was carried out while the brewery continued its operations. “It was literally like open-heart surgery. Carrying out upgrades to the facilities of an operating brewery mid-season means you have to make use of any non-productive times, so we were there on lots of Saturdays and even Sundays. corosys was also willing to carry out the commissioning at the times we prescribed. That’s something we can’t stress enough,” Dahncke continues.
Thanks to the new mixing system, the company is now well equipped to handle any developments in the next few years. With the option of being able to mix two products in parallel, it can keep pace with the anticipated growth in mixed beer beverages and non-alcoholic beverages with sufficient production capacity.

Conclusion
It is no secret that the focus is shifting more and more toward non-alcoholic beverages and non-alcoholic beers. The trend is clear to see, and now is finally the time for many producers to rethink and optimize their established processes and make them even more flexible. That doesn’t necessarily mean that new systems need to be purchased. Converting an older system or integrating new elements into an existing process can offer just as much flexibility. The example provided here demonstrates how this can even be done during ongoing production. Paulaner is glad that it took this step early on and can continue to produce efficiently.
Would you like to find out about current trends on the beverage market and exchange professional information? Then we invite you to take part in the next drinktec, which will be held in Munich from September 12 to 16, 2022.
This article is powered by BRAUWELT.