Themed week Product Safety: Aseptic cold filling meets consumer demand
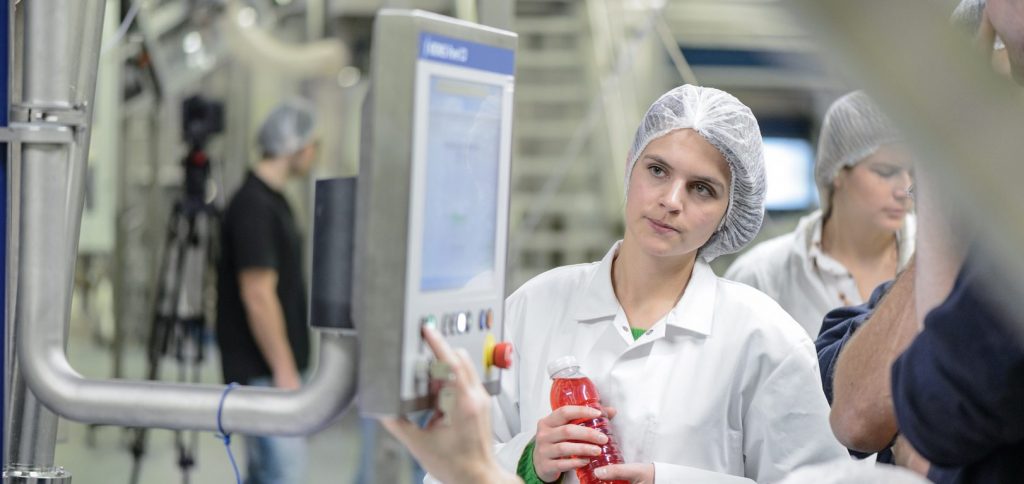
Demand for sensitive beverages, such as fruit juices, isotonic drinks and milk mix products, is on the rise. More and more sensitive drinks are being filled into PET bottles, which weigh a lot less than glass bottles. No matter the container, product safety remains the top priority.
Health-conscious consumers have their own expectations: plenty of vitamins, a rich variety of other healthy ingredients, and no preservatives. Of course, all of that needs to be done without compromising the product’s taste, look and freshness.
Dry heat sterilization versus moist heat processing
Health-conscious consumers can have all of their demands met thanks to aseptic cold filling in PET disposable bottles. There are two approaches to the process: dry heat sterilization, which involves using hydrogen peroxide, and moist heat sterilization, which uses peracetic acid.
When it comes to moist heat sterilization, the traditional process of rinsing the bottle happens after the sterilization phase, before it goes on to be filled. In the case of dry heat sterilization, however, there’s no need to rinse the bottles with sterile water. This process offers many advantages. For example, you don’t need to use as much water, air, electricity, and sterilizing agents. In addition, less space is required for plant technology, and the changeover times are reduced when switching between products.
It’s the details that count when it comes to the plant manufacturers’ procedures. For example, some already have a set sterilization procedure for preformed bottles; meanwhile, in other systems the sterilization process only takes place after the plastic bottles have been blown. Sterilized preformed bottles are generally kept within a sterile zone, which prevents recontamination and seals the plastic bottles with sterilized caps immediately after being filled.
Beverage companies prefer sourcing everything from a single provider
Manufacturers of aseptic cold filling technology often offer processing technology that can take care of this step as well. Many beverage companies have recognized the advantages that come with ordering everything from a single provider: Within the already complex realities of aseptic systems, they only need one contact person for the whole aseptic process.
These days, it’s possible to develop a plastic bottle that’s tailored to a specific product or brand. These customizations build on top of the basic requirements that the bottle should not weigh a lot, it should be sustainable and, at the same time, cost-effective. More advanced bottle concepts take into account the product itself and its shelf life as well as production conditions and how they are handled during transport and at the points of sale.
Hot fill manufacturing as an alternative
Another approach to safely filling sensitive nonalcoholic beverages is the hot fill technique. There’s one major advantage to this filling process: The investment costs are lower than those for aseptic processing. In the fields of energy and PET bottles, however, there are additional operating costs that need to be taken into account. The decisive point for the consumer is that hot fill bottle manufacturing does not preserve the same quality, taste and vitamin content of a drink to the extent that aseptic cold filling does. The argument against hot filling for the more expensive plastic bottles, however, was recently blown out of the water to some extent. By feeding nitrogen into the headspace of hot-filled PET bottles, manufacturers can prevent the bottle from shrinking after filling, meaning they no longer need to rely on the more expensive cold fill process. In addition, vacuum panels are made redundant, which results in bottles weighing a lot less.
Aseptic cold filling: The need for further development
Aseptic cold filling is the future: With demands for healthy, natural foods on the consumer side, it seems likely that beverage manufacturers will rely more and more on aseptic cold filling in the future. As consumers demand an increasingly wider range of beverages, suppliers need to develop innovative solutions to deal with even faster changeover times. When it comes to processes and bottling, there’s also an emphasis on cost reduction.
At this year’s drinktec, you’ll find plenty of exhibitors on site who are eager to talk about innovative nonalcoholic beverage concepts, individual, lightweight PET bottles and aseptic cold filling. For example, at the PETpoint, in Hall A4, exhibitors will be showing machines alongside the raw materials used for producing plastic containers and seals. There, you can also discover all kinds of recycling solutions. In the Innovation Flow Lounge and at the 5 O’clock Theme area, visitors can find out more about aseptic cold filling. In conjunction with the themes of process technology for safer drinks, new raw materials and lot size 1, the drinktec forum offers further insights into the world of aseptic cold filling.
The Innovation Flow Lounge is supported by:
- Döhler
- FoodBev Media
- KHS
- Sahm GmbH
The 5 O’clock Theme is supported by:
- KHS
- SIDEL