Conserving resources – boosting efficiency: the order of the day
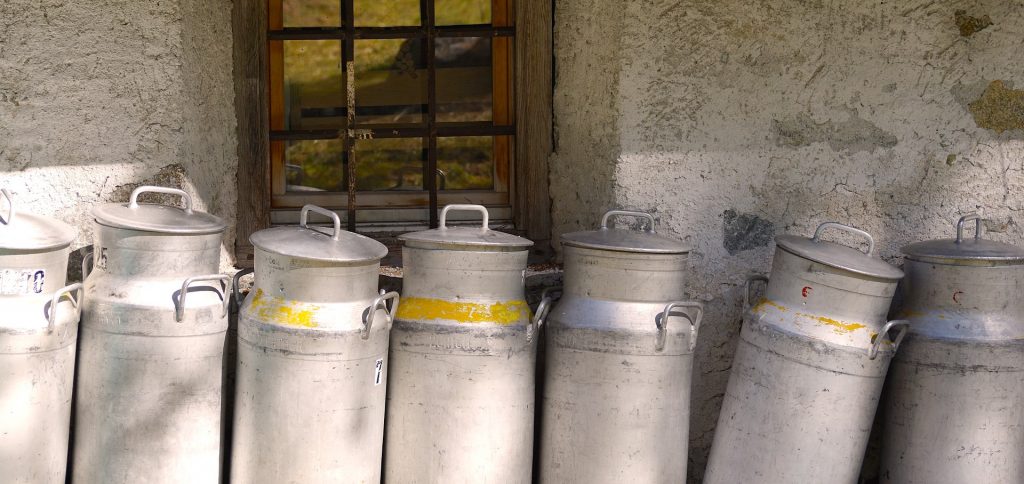
Conserving resources and improving the efficiency of the entire company while meeting today’s sustainability demands – this is now the top priority of every production process. A company that makes its successes in sustainability publicly known and demonstrates how truly “green” it is may more successfully be able to distribute its products to consumers.
With one qualification: Marketing, the product concept, the price, packaging and advertising promises directed at consumers also have to be aligned. Any company wanting to avoid the shadow of suspicion that could be cast on it by the media has to communicate in a manner that is based on hard facts. The public also has very little patience with jargon and greenwashing – and the decision to not communicate at all is simply unthinkable.
Only individual approaches create solutions
There are as many ways to conserve resources as there are dairies. Sure, all process-technological companies have a few general things in common, namely energy and material consumption. Implementation of conservation steps will always be done individually. After all, the willingness of the industry as a whole to invest in conservation measures whose positive effect will become evident only over the long term, and not the short term, differs widely. When companies discuss ways to conserve energy and resources, the same argument about ROI always comes up: that it isn’t immediate enough in the short term.
Conserving resources becomes more complicated
It must also be noted that things are becoming more and more complex. Every individual measure, such as the recovery of heat energy in wastewater, must be viewed in a larger context: If it fits into the concept, the “effect” can be used at all times throughout the year. How do individual measures impact total energy performance, and how can this be measured? These considerations bring us back to the Industry 4.0 approach and the question regarding the availability of systems throughout their entire service lives. The means to carry out Industry 4.0 already exist. Depending on the operation itself, it will take six to 10 years for Dairy 4.0 to have been implemented completely.
The lines have to run
Let’s focus instead on the availability of systems. In this regard, many positive effects can be achieved at most companies, say experts such as Axel Keller of AKR Engineering in Wedemark. In the future, all dairies must define reliability as a core skill and even invest in it if they wish to keep up with the generally well-positioned industry leaders in terms of production costs.
Increased protection from breakdowns is provided by a holistic arrangement of system instrumentation, the use of smart sensors, disciplined commissioning and reliability-focused assembly of the periphery (e.g., pumps). Certain requirements must be met in terms of maintenance as well, including the development of status-oriented and preventive concepts and care during planning (travel times, etc.). Maintenance, an area that used to be viewed as a cost driver, is really one of the key functions for a cost-cutting form of higher availability and, thus, the efficiency of systems.
Resource conservation and system availability have also played a major role at drinktec, even if exhibitors may not have talked about it so explicitly 10 years ago. Until the next drinktec is held, companies in the supplier industry will have ample time to come up with new innovations and enhanced products. We are looking forward to seeing the clever and exciting solutions that will be presented from September 13 to 17, 2021, in Munich!