Operational energy management in dairy plants: To start with, measure diligently!
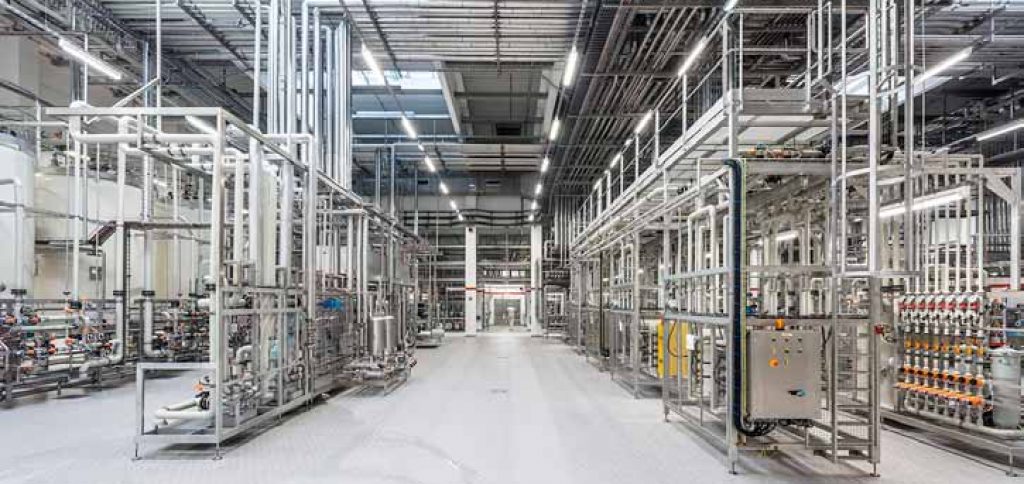
Sustainability, resource conservation or merely cutting energy costs: The motivations for efficient energy management are diverse. But where does one begin when many dairy plants don’t know a thing about either their energy flow or their energy consumption? And then there are the costs of the technical equipment for saving energy. Knowing when, where and how energy is consumed in a dairy plant is a prerequisite for efficient energy management. This is the only way that dairy plants can successfully minimize their energy consumption.
Measuring energy consumption correctly
Above all, those responsible at the plant must consider what they actually want to measure and ultimately achieve. Mere kilowatt values for energy consumption are not enough. Dairy plants must put their energy consumption into an appropriate context—such as in relation to the quantity of milk, whey or cream processed or in relation to production or infrastructure systems. Dairy plants should not set up or purchase a measuring system to record the relevant data until after this step.
Assessment criteria for measurements
To catch rogue results and avoid being unpleasantly surprised—or have to admit that they acted inappropriately—dairy plants should clearly define the measuring period. There are also technical facilities that one cannot influence that should be excluded from further consideration. After all, if you can’t change it, then there is no need to measure it.
Cut costs with successful energy management
Measuring and recording energy consumption costs money. Anyone who wants to succeed, i.e. to optimize energy management in the long term, also needs to take continuous measurements that are accurate in every detail. This clearly means that the possible potential of cutting energy costs must be sufficiently higher than the costs of the required measuring system including the expense of installation.
Caution in old dairy plants
Those who have older plants might also have problems with existing interfaces. Proprietary interfaces that were commonly used in the past do not generally allow the cross-system exchange of data. These old, “dead” interfaces can only be replaced by new equipment. That is something people should know before rushing in to measure energy consumption. Admittedly, given their level of automation, most German and European dairy plants are state of the art when it comes to IT anyway.
drinktec, the World’s Leading Trade Fair for the Beverage and Liquid Food Industry, is the perfect platform for exchanging information on the topic of energy management. Guests attending the fair can gather information on energy-related topics, especially in exhibition halls A3, B3 and C1. They can also get an overview of the latest hot topics that pertain to the milk industry on Focus Day: Milk on September 15 in Hall A2. In addition, the drinktec website and the drinktec App feature plenty of tools to help you prepare for a tour of the exhibition in a targeted manner.
More articles about the milk industry and liquid food are available here.