The digital transformation in the beverage industry
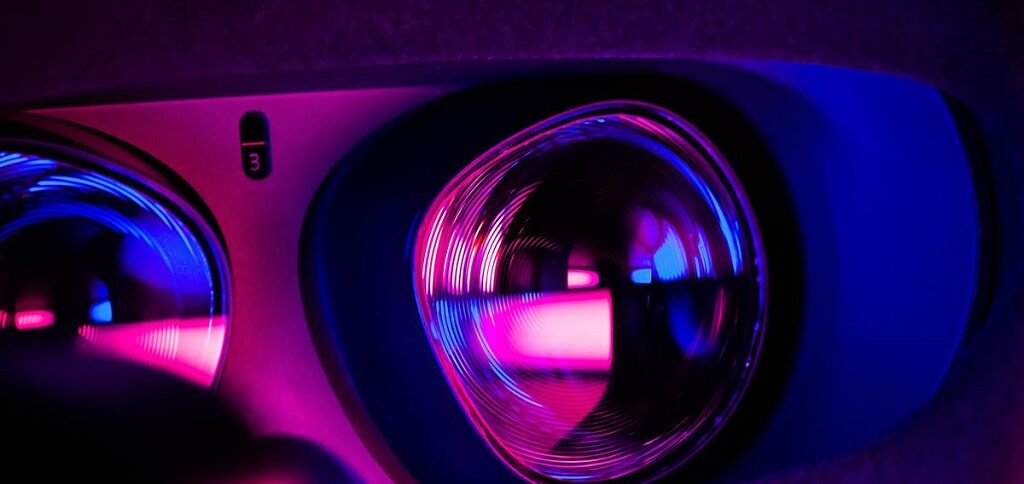
The global pandemic has spotlighted the food and beverage sector. In particular because fluctuating customer requirements and closed borders strained supply chains to their limits. Reda Mostafa, Business Development Director at PTC, explains here how the digital transformation of the food and beverage industry can help it operate successfully, even in such unpredictable times.
Seize opportunities with a consistent data strategy
The food and beverage industry is under immense pressure. Changing requirements must be managed, and simultaneously industry leaders must try to reduce costs, increase innovation as well as improve quality and, above all, transparency. Digitalizing the beverage industry stands out as the best solution for these challenges. The trend has been approaching for quite some time, but today’s opportunities regarding increased process transparency and the detailed business insights that can be gained from consistent data strategies are more relevant than ever.
React flexibly to process changes
The high quality demands mean that many manufacturers have developed systems for securing every step in the supply chain. However, these measures are often highly individual, intricate and expensive. Changing customer requirements or the processes themselves are often met with structures that grow in complexity and generate intensive adjustments with high costs and revenue losses due to their inflexibility.

Selecting applications individually
Before the COVID crisis, the beverage industry was focused on improving overall equipment efficiency (OEE). Since then, the problems must now be solved in dramatically different ways. Today, everything revolves around Industry 4.0, and with it the Industrial Internet of Things (IIoT) and augmented reality (AR) platforms. Moreover, each company faces their individual challenges in this area. Different use cases require targeted, individual measures to drive the digital transformation effectively.
“Keep the lights on”: Digitalized beverage industry opportunities
What do you do when employees with expert knowledge must work remotely or even go into quarantine? How can you secure production flows if the experts aren’t on site in an emergency?

Two relevant solutions exist: The first is simple prevention by creating digital work instructions and process descriptions that can be flexibly edited. This provides opportunities to use AR. In the second solution, experts can use a remote solution, such as Vuforia Chalk, to visually guide the colleagues working on site via smartphone or with AR/MR glasses to quickly identify or eliminate errors and clarify quality controls in real-time. There is also the need to prepare relevant information regarding production based on roles, even outside of production – in real-time and without costly data processing.
This is one of the strengths of the world’s leading IIoT platform, ThingWorx [1]. Everyone in the company has access to both the simple, innovative handling when consolidating data from a wide variety of sources, along with the automation pyramid (connectivity) and the creation of individual dashboards or AR applications. ThingWorx promotes digital transformation through new concepts, such as “Citizen Development”, by offering its own configuration methods and open low-coding structures. For example, the applications can be easily created using the drag-and-drop principle. This can help bring the respective IIoT projects to fruition faster and more cost-effectively.
There are numerous predefined out-of-the-box (OOTB) solutions, such as for real-time monitoring, condition-based monitoring, predictive analytics for quality and maintenance and energy management.
Connecting machines across systems
Real-time production control and analysis requires continuous information from every machine and device. After analyzing production data, the production line can be optimized and secured so that the manufacturing systems work efficiently. This will only work if the devices communicate with each other, even if they aren’t from the same manufacturer or support the same protocol. For this particular beverage industry digitalization challenge, KEPServerEX offers the possibility to define links between data values in different data sources, which enables machine-to-machine communication (M2M) that is as close to the device as possible.
Standardizing via connectivity platforms

The standardization of operational communication through a connectivity platform enables the quick connection of new devices and systems in modern production lines. It also simplifies the communication architecture; connects an ever-growing list of devices and provides support for legacy, current and future controller firmware and operating systems.
Most food and beverage manufacturers work according to the ISA-95 model, which is in line with the automation pyramid, inside of the factory. ISA-95 intends to provide a consistent terminology that forms the basis for manufacturer communication and provides compatible information models and consistent operating models. Within this stack, each layer – from the machine sensors to the business systems – only communicates up or down one layer at a time. This is where the connectivity platform – equipped with adapters for various programmable logic controllers (PLCs) from every manufacturer – comes into play. Then, the data collected through this method can be processed in an IIoT platform to create role-based applications or dashboards that provide the necessary insights.
Digitalization at Carlsberg
Carlsberg uses the ThingWorx IIoT platform in combination with Microsoft Azure in 28 breweries in Europe and Asia. The solution lets the company track its global operations transparently and document the transformation of raw materials into finished goods, as well as provide detailed analysis of the packaging cycle. Production managers in the 28 breweries and headquarters analyze the processes in real-time.
The plan is to build an end-to-end value chain that affects everything from forecasting to sourcing, brewing, packaging and logistics.
With over 40,000 employees worldwide, the company uses the technology to monitor critical packaging lines, tracking overall line effectiveness and performance, thereby ensuring greater product and production consistency.
Factory benchmarking via beverage industry digitalization
At its core, digitalization depends on standardizing all of the data that flows into the company view. This enables the comparison of factories with one another and more flexible reactions to changing market requirements.
Another important point is increasing factory performance, for example when a line changeover is planned. AR applications can be helpful here. This allows for an experienced employee to create an AR application that guides younger, less experienced colleagues through individual processes. This increases efficiency, minimizes errors and makes individual processes traceable. Furthermore, it keeps valuable knowledge within the company, even when older colleagues retire.
Another increasingly important area in beverage industry digitalization is the overlaying of 3D data onto real plant components or areas. For example, a visual 3D model (CAE/CAD) in a traditional AR overlay does this to guide the person either during a line changeover or during plant maintenance.
Conclusion: Accelerate digitalization intelligently
All companies – be they global manufacturers or regional special producers – keep an eye on their product yield and quality. In each case, factory performance data should be used to make informed decisions and boost repeatability to keep the factory operating both profitably and for a long time.
Ultimately, digitalization depends on understanding what exactly must be achieved from a strategic perspective, as well as what must happen or be prevented in the factory. Then, the expected value of the transformation project must be realistically calculated: How big is the impact? By how much can we reduce the line changeover time? How much more uptime can we expect? Can the initiative be scaled across the factory, and, in the future, across multiple factories? IIoT platforms hold the answers to these questions and many more. Moreover, the right partner can help with planning and answering these questions.
Sources
[1] PTC has been recognized as a leader in Industrial Internet of Things (IIoT) solutions in four major analyst reports:- The “Smart Manufacturing Platforms Competitive Ranking” study from ABI Research
- Report (Q3 2021) of “The Forrester Wave: Industrial IoT Software Platforms”
- “IDC MarketScape” report on industrial IoT platforms and applications for manufacturing
- Gartner “Magic Quadrant™ for Industrial IoT Platforms” report
Want to share your developments and innovations in the beverage industry to an international specialist audience? Then we would very much like to invite you to take part in the next drinktec from September 12 to 16, 2022 in Munich.
This article is powered by BRAUWELT.