Brewhouses: Global innovation drivers
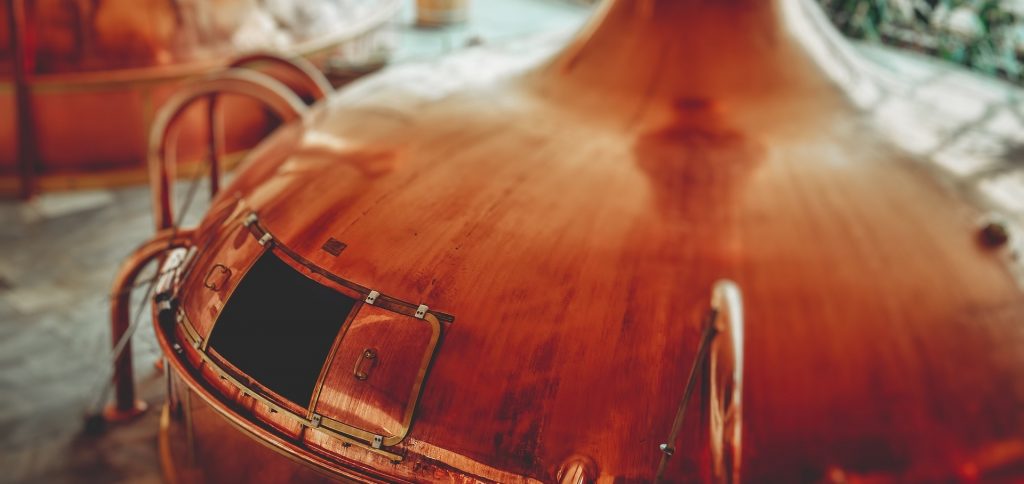
Manufacturers of brewing equipment and systems are increasingly having to respond to the individual wishes of new target groups. And size is not always everything: Small, state-of-the-art brewhouses are enabling Krones AG, Rolec, and others to tap new markets around the world.
When it comes to modern brewing equipment, German providers have been the ones to lead the way. Every brewer knows Krones AG, Ziemann Holvrieka GmbH, GEA Brausysteme Group, and Rolec – Prozesse und Brautechnik GmbH. They’re all renowned manufacturers that have installed their brewing systems in brewhouses around the globe while focusing on process optimization, energy efficiency, digitalization, flexibility and.
Pioneering modern brewhouses
The Franconian brewery Schlossbrauerei Reckendorf opened one of Germany’s most state-of-the-art brewhouses this year. Ziemann Holvrieka GmbH, based just north of Stuttgart in Ludwigsburg, has been providing customized solutions for the development, manufacture, and installation of stainless-steel containers for the drinks industry for the last 165 years, and has developed a special mash filtration procedure featuring a completely new process for extracting wort. Omnium by Ziemann, as the product is known, celebrated its world premiere at the previous drinktec and was inaugurated in Reckendorf just a few months ago. The key innovation of the Omnium brewhouse is the Nessie by Ziemann mash filtration system, which uses a novel separation and extraction procedure to transform the lautering process. This new process promises shorter process times, higher yields and lower costs.
Thanks to its four sequentially connected rotary disk filters, the system can separate the spent grains and wort, employ turbulent counterflow extraction, and dynamically wash and separate solids. “We decided in favor of the Ominum brewhouse essentially because of its much greater flexibility,” says Reckendorf’s master brewer, Dominik Eichhorn. The equipment also allows him to intervene in the individual steps of the brewing process to get the best results in terms of yields and valuable ingredients.
Further proof the Ziemann Holvrieka team embraces innovation challenges to achieve better solutions for their clients comes from the Piedras Negras 2.75 project at the Mexican brewery Compañía Cervecera de Coahuila. The brewery has expanded to a total capacity of 27.5 million hectoliters and is now one of the world’s largest and most state of the art.
Big and sustainable can go together
Another example of record-breaking brewhouses is the new Guinness St. James’s Gate brewery in Dublin, which has vessels designed for a brew size of up to 1,000 hectoliters. Sustainability was the top priority in deciding to construct the brewhouse, which has seen impressive energy savings: The brewhouse consumes up to 45% less steam, 33% less electricity and 35% less water in the brewing process. This is all achieved thanks to the “Steinecker EquiTherm” from Krones AG, a market leader in filling and packaging equipment for beverages. With a capacity of more than 8 million hectoliters, St. James Gate is now the world’s largest stout brewery. Krones AG supplied three brewing lines, including Europe’s largest lauter tun in Brewhouse No. 4.
The same system from Krones AG is also used by Austrian brewery Murauer. Before switching to “EquiTherm,” the company consumed some 700,000 liters of fuel oil a year. It has now reduced this consumption to almost zero. It did this by switching to low-temperature process heat in the form of hot water from a wood-heated biomass cogeneration plant operated by Murauer Stadtwerke GmbH as well as by using the Krones system. The energy required for mashing is provided by the wort cooling process.
Replicating global processes
In the Bavarian town of Attaching near the city of Freising, Krones AG opened one of the world’s most state-of-the-art testing and research brewhouses this year. The Steinecker Brew Center boasts brand-new equipment and cutting-edge process technology. The five-hectoliter brewhouse facility comprises five different vessels and allows the Krones team to replicate any beer-making process used anywhere in the world. This means the company can develop improvements for well-known brewers in Africa, Argentina and the Philippines. The facility showcases, for example, different equipment surfaces that have been sandblasted, ground or insulated. The customer can also localize, in real-time operation, innovative heating solutions with high-pressure hot water as well as all vessels. “This is an important innovation for us, especially as we have seen a big change in the customer structure in recent years,” says manager and master brewer, Johannes Eymess. “More and more brewers are coming to us who want to work with smaller brewing equipment.”
Influence of the craft beer movement
Equipment manufacturers are increasingly responding to the international craft beer movement now. The growing numbers of creative brewers need smaller brewhouses. Braukon GmbH, Kaspar Schulz Brauereimaschinenfabrik & Apparatebauanstalt GmbH and GEA Group have all embraced this trend. Düsseldorf-based GEA, a technology company with an international presence, focuses on process technology and components for new production methods. Alongside the Compact-Star brewhouse line for medium-sized brewers, GEA is now offering a new brewhouse, “Craft-Star,” for specialist artisan brewers. GEA describes this as the perfect tool for the artisan brewer wishing to produce 40 hectoliters of wort in any style.
Integrated systems in the Craft-Star monitor the differential pressure and provide full control of the lautering process. The automated Gearboxx system is designed to ensure repeatable batch production, process visualization and remote support. According to the manufacturer, the GEA process delivers up to 98% extract yield in the lauter tun. The system is already operating successfully at Brouwerij Anders in Halen, Belgium.
Customized, turnkey systems
Rolec – Prozesse und Brautechnik GmbH in the southern German town of Chieming is also concentrating on the international craft beer scene. The company has already supplied many successful brewhouses, such as Brewdog in Scotland, Meantime Brewing Company in London, Lion in Adelaide, and the Brooklyn Brewing Company in New York, delivering customized, turnkey systems for their customers’ entire production processes. One of its latest projects is now on the launch pad in Waakirchen in southern Bavaria: Specially developed by Rolec for Markus Hoppe, the boss of Hoppebräu and a local craft beer entrepreneur, the brewery was exhibited at the most recent drinktec.
Hoppe’s modern brewhouse with a cast-out wort volume of 20 hectoliters features a decentralized mixer that turns the mash into a 100% homogeneous mass faster than a conventional plant. This prevents clumps forming, even without the injection of oxygen. A wort boiler means the brewer is not reliant on the wort level in the tun and can heat the first wort on its own using an external boiler. There is also a height-adjustable chopping system, a larger lauter tun for specialist beers, an enlarged whirlpool for hoppy beers, and a Dryhopnik system that accelerates the dry-hopping process and increases aroma extraction. The system ensures the whole tank is well mixed and a homogeneous beer with high flavor stability is produced. Hoppe is not only counting on high quality but also documentation true to the Industry 4.0 model. The BrewMax control system displays all the important data at a glance. “I think it’s extremely important that equipment manufacturers are now also engaging with what smaller breweries are looking for,” Hoppe says. “For me, technology and innovation are the key factors.”