Optimized cleaning — only when needed
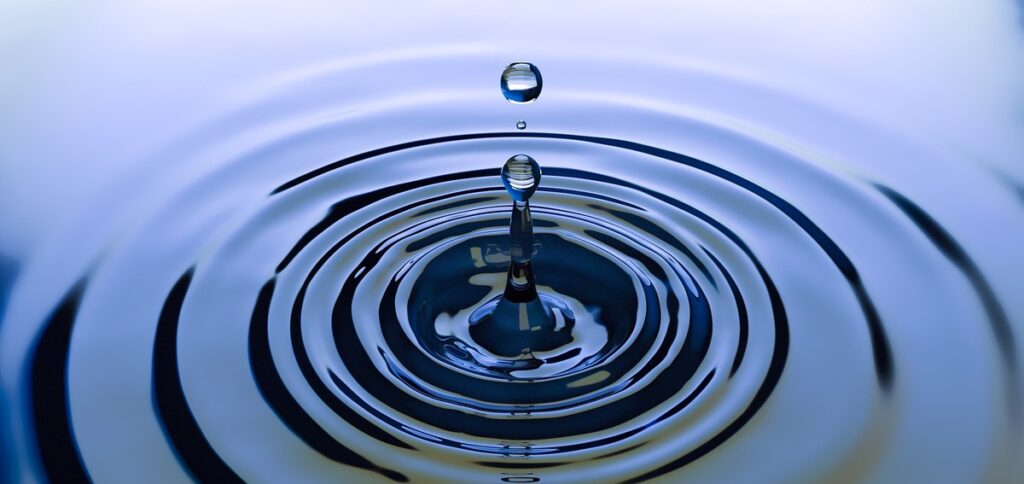
Needs-based cleaning is now often considered a foresighted concept for a new approach to cleaning. But what does this involve? How do we define the need for cleaning? Martin Löhrke, CEO of the Lübeck-based Jürgen Löhrke GmbH, provides his insights into the options already available today for meeting the requirements of individual cleaning.
Boost production efficiency with intelligent cleaning concepts
People around the world are engaged with such crucial topics as the shrinking water table, environmental protection, rising energy costs and the increasing scarcity of resources. Yet in the face of this, particularly beverage and food producers still have to continue to ensure the supply of food and beverages. The demand for sustainable products and more environmentally friendly manufacturing processes is growing at the same time. Along with these issues, business factors require consideration, as cost and price pressure continues to rise. System efficiency also must still be ensured and the highest possible productivity achieved.
Needs-based cleaning? What does that mean?
Needs-based cleaning can be described as a cleaning intensity based on the contamination level of a system. The associated cleaning concept draws its definition from the Sinner’s Circle, which illustrates the necessary parameters for a successful cleaning. These considerations focus on the influence that the contamination and the process technology of the equipment to be cleaned have on the cleaning result. To ensure effective, economic cleaning, mechanics, temperature, time and chemicals must be systematically deployed. If one of these factors varies, another factor must inevitably compensate for the difference.

Consider all subprocesses
Often, the overall contamination is a primary consideration, but not the individual process steps and their different levels of contamination. But to optimize the cleaning process, it’s essential to more closely examine the subprocesses and their contamination and to adjust the cleaning parameter accordingly. The Sinner’s Circle is also well suited to use as a basic framework to accomplish this.

How is the need for cleaning defined?
In beverage and food production, cleaning is often carried out in strict accordance with a hygiene concept. This concept usually has cleaning scheduled after a certain production time or after a product change. It usually disregards the actual need for cleaning in the production process, despite the considerable potential for optimization.
The following image shows the contamination measured when filling products A, B, C, D. The blue arrows show cleanings and flushings that follow the specified hygiene plan. The level of hygiene required for the system to ensure filling is microbiologically safe and therefore in compliance with the required best-before date is highlighted in orange. If these levels are exceeded, the safety of the product cannot be ensured.

Cleaning effort vs. need for cleaning
The cleaning effort involved can now be compared with the actual cleaning requirement, as shown in the following figure. After production, standardized cleaning takes place according to the specifications laid out in the hygiene plan (orange line). This usually does not correspond to the actual contamination level of the system after the end of production (small green bars). While the cleaning parameters for the contamination of products A, B and D are overvalued, the polluting load of product C exceeds the cleaning performance of the specified parameters. This means we can’t rule out the possibility that subsequent productions will be contaminated due to insufficient cleaning.

Hygiene monitoring and controlling
New sensor technology, such as biofilm sensors, makes it possible to monitor the development of biofilm. This technology can also assess mineral deposits. The results recorded were additionally examined via microbiological sampling in order to make assertions about product residues, deposits and contamination, providing an overall assessment of a system’s hygiene status.
Integrating the sensor into an adapted carrier system enables reproducible measurements. This way, hygiene-critical areas of the system can be continuously cleaned and disinfected as needed. Cleaning processes can then be optimized and long standard cleaning programs with risk buffers avoided, which leads to more safety in the product bottling process and newly won production time.
Needs-oriented cleaning: Methods and advantages
Needs-based cleaning isn’t a topic for the future. Even today, many companies are observing that systems in different sections show different degrees of contamination. Thanks to optical methods such as camera systems, fluorescence analysis and other measuring technologies, particularly critical sections in the production process can be identified and examined. Sensor technologies available today monitor parameters such as temperature, flow rate, conductance, pressure, pH value and redox. Newer sensor technologies also measure biofilm and contamination.
Coordinate not only when, but also how to implement differentiated cleaning
Integrating a biofilm sensor into the process is the recommended step for supporting detailed process observation. The sensor can be moved in a network-like manner using a carrier system to provide many measuring points. This makes it possible to establish differentiated and needs-based cleaning tailored to the production process. The cleaning cycles (frequency) and the formulation of the cleaning media (chemical products, concentrations) can be precisely adapted to the respective production phase using the biofilm and additional microbiological tests.
Depending on the object, developing special solutions for particularly problematic areas is also advisable as is holistic cleaning. In addition, focusing on the lowest possible chemical concentrations, efficient application times and optimized, low cleaning temperatures in the concepts is recommended. When it comes to chemicals, the user is free to choose the best chemical product for their particular application.
Summary
Real-time measurements are becoming more and more relevant. Environmentally friendly cleaning concepts and conservation of resources are important. Using biofilm sensors, companies can record and collect data about their production process as well as visualize and analyze the data using software. Using modern technologies for process cleaning optimizes the consumption of valuable resources such as water and energy and minimizes the use of chemicals.
Would you like to find out about current trends on the beverage market and exchange professional information? Then we invite you to take part in the next drinktec, which will be held in Munich from September 12 to 16, 2022.
The article is powered by BRAUWELT.